The Keys to Understanding Cultural Lean
Standardisation and Innovation: Navigating the Paradox
Standardisation and innovation: Navigating the paradox
During a conference on my book in Rennes in October 2022, an audience member asked a pertinent question. He found the content interesting, but struggled to see how to implement Lean in his small team, believing that standardisation would significantly hinder his team’s creativity.
This is a relatively common misconception in individualistic cultures, where standardisation and innovation are often seen as opposing forces. At first glance, standardisation is perceived as a constraint on creativity and entrepreneurial freedom. Paradoxically, however, standardisation, like innovation, is the basis for continuous improvement. The crux of the matter lies elsewhere: in the framework within which improvement takes place.
Before going any further, it is important to clarify what we mean. A standard is defined as the best known method at any given time. It is dynamic because it is expected to evolve whenever a better method emerges, whether in three days or five years. Other characteristics of a standard include its derivation from stakeholders, its basis in field observations, its implementation through incremental experimentation, and its ultimate service to the customer.
So it is not a case of “I decide to create my standard based on whim or inspiration”, but rather “I follow the existing standard to which I have contributed until we collectively decide to change it for a better method”.
Standardisation therefore operates within a collective framework. To caricature a bit, we might say that the driver of individual innovation is to differentiate oneself from others, from colleagues – which is perfectly legitimate – whereas the driver of collective innovation is to outperform the competition.
What do we need in a collective creation process? Firstly, a common and shared language (the standards) between teams. Second, temporal milestones, i.e. periods of time during which these new standards can be tested.
In reality, standardisation and innovation are not mutually exclusive. They are complementary, forming the two poles of continuous improvement, like two sides of a coin that cannot exist without each other.
Individualism versus collectivism
This dimension reflects the extent, degree and nature of the ties between the individual and the members of the group. It refers to the concept of identity formed in relation to others.
In so-called ‘collectivist’ cultures, people exist through their membership of a community, so that the interests of the group take precedence over personal interests. This orientation refers to a society in which people are integrated into a community from birth. In these cultures, social harmony takes precedence over independence and individual expression. Confucius aptly illustrates how individuals invest in these roles: “I am the totality of the roles I live in relation to another particular person… Taken together, these [roles] weave for each of us a unique pattern of personal identity, so that if some of my roles change, the others will necessarily change and make me a different person”.
You may have heard the anecdote about the Japanese man who introduces himself by first stating the name of his company or institution. Then he mentions his department, followed by his position and finally his name. In Japan, everyone exists in relation to others. In fact, there are three different ways of saying “I”: Watashi (私), Boku (僕) or Ore (俺). The choice of pronoun depends on the context of the conversation and the person you are talking to.
As for me, I never introduce myself by talking about others. I start by talking about what makes me who I am, what I do or what I have (such as my job title), because I come from an individualistic culture, typical of Western societies, where the degree of attachment to a group is much weaker and where personal fulfilment, freedom and well-being prevail over the group. This construction of identity comes from Greek philosophy, which advocates the ideal of a free individual: master of his life and choices. It results in an identity more independent of others.
From Organisational Chart to Flow Diagram
Lean originated in Japan in a collectivist culture where individuals identify themselves through their different roles. With these elements in mind, we can better understand the central role of the flowchart in Lean. Whereas individuals from Western cultures might turn to the organisational chart to identify their role, in Lean the focus shifts to the flowchart. It is less about identifying people by their job titles and more about their roles in relation to others in the value chain.
Virassack, a young planner, quickly discovered this at Toyota Motors Europe. On arrival, he joined the Supply Chain Management department and set to work on his new responsibilities. A few weeks of intense integration and learning later, Virassack was invited to a one-on-one lunch with the then Vice President of Toyota Motor Europe: Mr Tadashi Arashima. Both honoured and nervous, he had no idea what they were going to talk about.
Virassack tried to put on a brave face during the car ride to the restaurant. Although Mr Arashima broke the ice to put him at ease, the idea of talking to such a prominent figure made him a little uncomfortable. Arriving at the restaurant, they continued to discuss general matters until Tadashi Arashima asked him a question that would have a profound effect on Virassack: “Do you know why your role is important, why you are here, and how you will contribute to the organisation?
Surprised by the directness of the question, Virassack replied that he thought his job was mainly to manage data and produce error-free planning files. Looking back, he smiled at his naive answer, but at the time he genuinely believed it was the right one. Mr Arashima kindly explained that planning at Toyota was much more than a simple administrative task. “Planning at Toyota is a strategic activity,” he said. “Every number you enter into our systems is not just a number, it is a commitment.”
Virassack listened intently, gradually realising the extent of his responsibility. Arashima continued, “Your estimates and schedules directly contribute to management decisions. Your work has a real impact on our entire supply chain and therefore on our overall success.
The moment was a revelation for Virassack. He realised that each employee’s role was an essential cog in the machine. Every task, no matter how insignificant it might seem, had its importance in the whole. This awareness changed his view of his work. He was no longer just a data planner, but a key player through his role in a larger organisation.
Source: Lean Cultural Compass
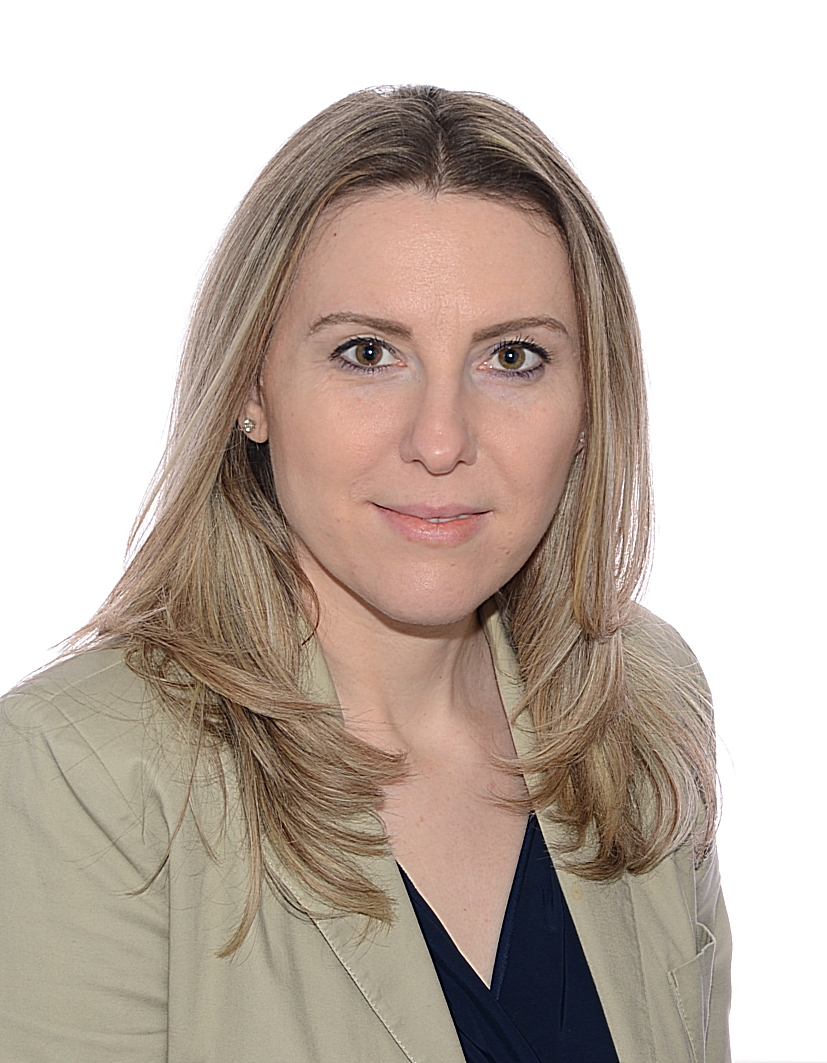
Natacha JUSHKO
Fondatrice du Lean Cultural Concept
Passionate about languages and discovering new cultures, Natacha Jushko has worked in business development and training for over 15 years. She now works in academic research in the field of management.
She has worked in Lebanon, Russia, China, and several African countries.
Author of “Voyage au Pays du Lean. Décryptage culturel et systémique du Lean Management!” published by Afnor (2021).