Lean training in West Africa: adapting for better adoption.
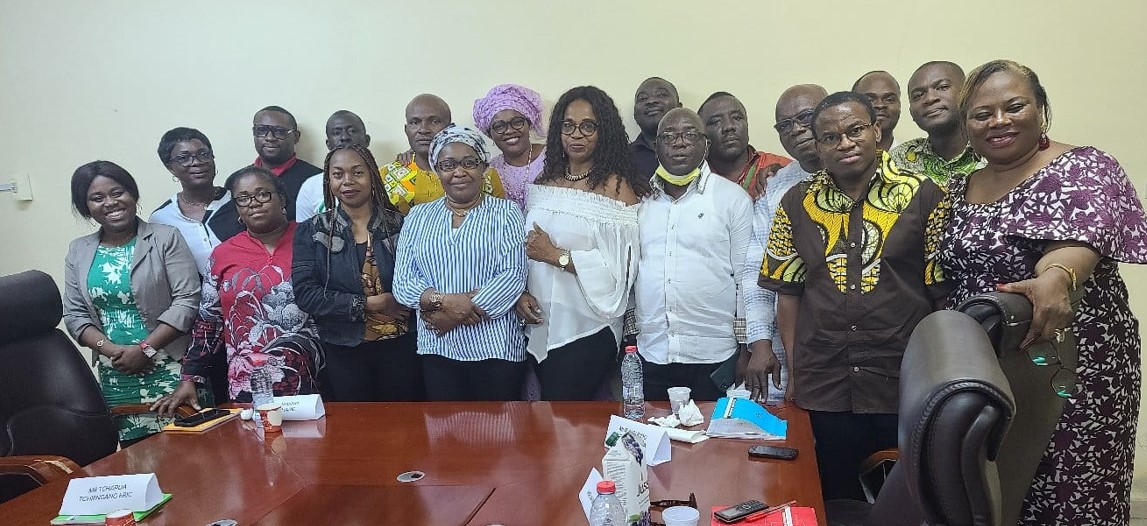
RΣ-THINKING LEAN #1
Insignts Natacha JUSHKO
Like the architects of Lean who have Japaneseized Western methods and contextualized them to the realities of Toyota, Lean actors tell us how they adapt the approach to serve organizations and teams around the world. Trained in the US, Karidja Sakango is a Lean trainer and consultant in West Africa. She talks about the interest in Lean on the African continent, the specificities of the cultural context to which she must adapt, and shares her tips for sustainably supporting organizations that are undertaking transformations.
Karidja Sakango is a trainer and consultant. She accompanies organizations that wish to adopt Lean in West Africa. She holds a master’s degree in accounting and financial sciences and techniques (MSTCF) from the University of Dakar-Bourguiba, and a master’s degree in science and project management from Walden University in the USA. She discovered Lean when she joined the airline caterer LSG Skychefs, a subsidiary of Lufthansa in the United States. In her role as Logistics and Operations Manager, she quickly realized the importance of flow and the need for detail. The company produces thousands of meal trays for various airlines and airports in an industry where every minute of delay costs thousands of dollars. She will launch Brains Consulting a few years later, in 2018. At the same time, she started writing a thesis on the potential impact of Lean culture in the effective and efficient management of resources in the public administration.
Lean trainings in Dakar, Yaoundé, Douala, Abidjan and Conakry
Globalization enhanced worldwide access to information leading to emerging new technologies promoting business management approaches like Lean, Agile, and Scrum on the African continent. Despite the enthusiasm these approaches can generate, they require progressive and rigorous actions for long-term results. Based on the pragmatism inherent to these new approaches, Karidja considered that it is not always easy to promote Lean as a managerial approach. She says: “Although business owners can be sensitive to the intent to manage resources efficiently and prioritize customer satisfaction, many companies still struggle to adhere to Lean management practices for two reasons. First and foremost, some organizations obviously don’t face competitive challenges. Thus, they don’t see the importance of continuously investing efforts to increase customer satisfaction when they have the monopole. Secondly, due to their financial and social situations, most consumers’ purchase decisions are based on price levels rather than quality and delivery time”.
Conscious that Lean management can contribute to a change of mindset regarding the importance of customer satisfaction, Karidja is sharing her knowledge through Lean training sessions in West Africa, from Dakar to Abidjan, through Bamako, Yaoundé, Douala, Conakry, and soon Bamako and Ouagadougou.
A transmission of knowledge to the antipodes
Karidja discovered the participatory approach when attending US Colleges and decided to embrace the field by launching a training and consulting company targeting exclusively west African companies. She will use this approach to ensure that, at the end of the training, the participants take ownership of the content to which they have contributed. Away from a standardized approach that would rather focus on certification processes, Karidja sets the framework and co-constructs with the teams. “I stopped preparing the second day of my training in advance. In the past, the content of my training sessions was fully written in advance, but I realized that it was a waste of time. I learned that a participatory approach is more beneficial. Each group is unique because each participant faces different issues. Together, we share different perspectives, look at issues from different angles using different skills, and create content that is actionable, based on Lean principles and techniques. I teach an approach, not a methodology. Thus, there is no recipe” explains Karidja.
Ultimately, Karidja adopts the posture of a Sensei, seeking to build the capacity of participants to find answers rather than having them learn a method. When she trains for the first level of certification, Karidja never defines Lean to the participants. Only at the end of the program she asks them to give their own definition. She has also set up a ritual to translate the term “continuous improvement” into the local language. For her, “It’s a matter of finding the words to convey the thought of adopting a continuous improvement mindset to make it their own. Doing so allows those who do not necessarily speak French and yet, play an essential role in the company’s value creation process, to better understand it“. This approach is even more relevant since linguistic researchers have demonstrated that the representation of the world is based on the languages spoken. For example, the participants of a multinational pharmaceutical distribution company in Dakar chose the Wôlôf expression “dém ba jeex” or “Dembadjeghe” which means “to give oneself to the fullest” to baptize this new way of working.
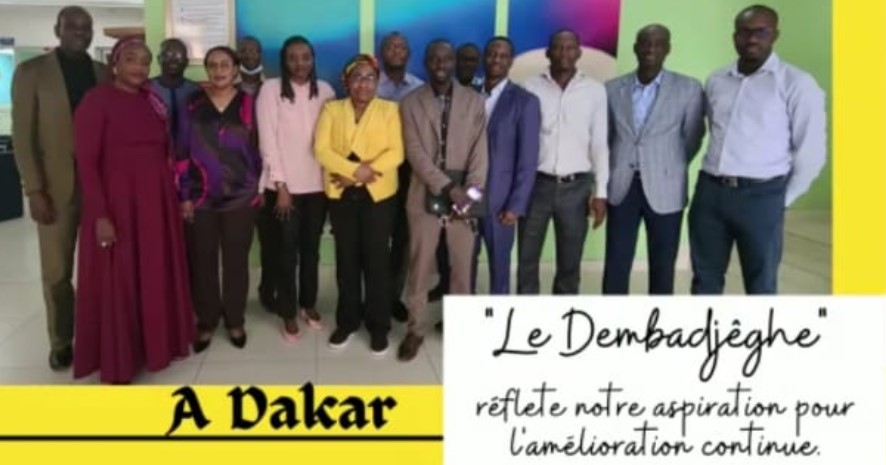
Brains Consulting Training, Dakar, Sénégal
And to illustrate the fact that the appropriation of the Lean approach also sometimes requires the modification of the original expressions, Karidja used to show a short video that presents how Lean management has found its place within Opinel SME, a French manufacturer of pocket knives.
Adapting training to cultural contexts
As she launched her business, Karidja realized that she would need to integrate some additional concepts. “The training courses I followed focused on Lean principles and tools, while change management and Lean leadership were not, because they were considered as already acquired. Unfortunately, that is not the case for my trainees“she says.
Creating a climate of trust to allow participants to express themselves requires face-to-face training. “I tried online training, but I quickly decided to stop. I need to see in participants’ eyes how they are receiving the message. To reach training goals, trainers need to create an inclusive dynamic by putting all participants at ease enough to say what they did not think they could express in hierarchically mixed groups.” She continues: “I focus on creating a framework beforehand that allows for the development of a culture favorable to implementing Lean.” Aware that one should not underestimate the obstacle that Lean can represent for certain managers who hold the information, which legitimizes their status and makes them right in the eyes of their subordinates, Karidja is strategic. “Culturally, the transmission of information has always been done top-down, so everyone receives the correct information to do their job effectively. Creating a bottom-up information flow diagram can be challenging, even though holding information is part of the hierarchical status. Her technique? Dedramatize and clarify the message.
From the organization chart to the flow chart
Karidja notes that companies that have adopted a Francophone management style are firmly attached to organization charts. She continues: “Unfortunately, organizational charts are the tragedy of our companies. We are attached to titles, to subordination, and relationships beyond the production of value”. So, to play down the framework, Karidja invites the participants to transfer from the organizational chart to create a flow chart.” It is the latter that materializes the contribution of each person in the chain of production of added value, which remains the company’s primary mission.
The challenge of visual management
Visual management can be a deterrent because it brings clarity and makes any lack of rigor visible. For Karidja, “visual management allows for real-time monitoring and establishes permanent rigor. Opacity, systematic non-formalization of procedures and many exceptions which confirm the rule that prevail in companies ran after the French management model, allow for grey areas that not everyone is ready to give up”.
Contributing to more Lean approaches in Africa
Here is Karidja’s wish. Once she has finished her thesis, she wants to invest her efforts in developing Lean management in public entities. Until then, she has set herself a new short-term goal, and not a small one, to organize a summit on operational excellence in Abidjan for the beginning of 2023 !