A Compass to Navigate the Lean Ocean
Lean management has a cultural tool: The Lean Cultural Compass (LC²)
The exploration of the cultural aspects of your company no longer requires the deciphering of sometimes complex cultural theories and is now fully integrated into visual management, which is an essential concept of Lean.
The need for a common language
Shall we consider, for instance, a key-value of Lean: compliance with standards. Let us imagine an observation visit (Gemba Walk) of your worksite environment. We will navigate through visuals such as Kaizen standards, work instructions, and other standards displayed in your area of activity. These standards are the best-known demonstrated way to perform processes. Now, let us address a purely human-oriented dimension: what is the connection between these norms and standards?
The so-called “universalist” cultures consider that a rule can be applied to any problem, regardless of the situation or context. However, the so-called “particularist” cultures examine interpersonal constraints and circumstances. Thus, the application of the rules is said to be “contextual”. Nonetheless, France is at the midpoint, for “the concept of the rule” prevails. This cultural dimension[1] is illustrated in the table below.
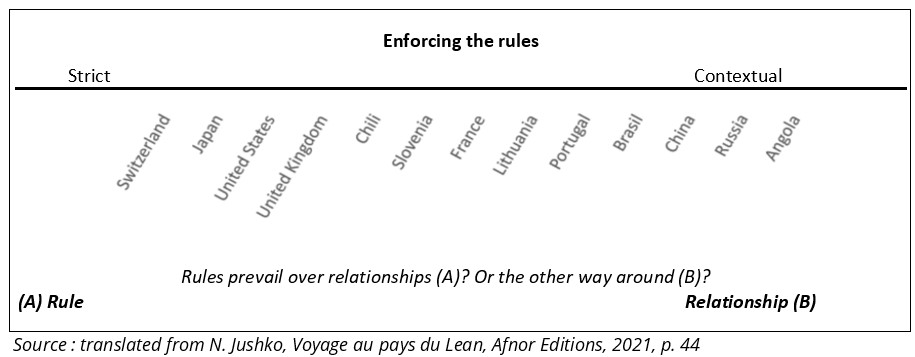
The very definition of “compliance with the rules” may be a variable geometry against a background of cultural dimensions. Does the application of standards vary according to circumstances? How relevant is the information displayed in the workspace? Is part of the furniture, such as the wallpaper, that we could come across on a daily basis noticing them?
Lean does not leave room for interpretation. We do expect the evolution of the standards, but within a determined framework: continuous improvement. Therefore, establishing a common cultural language is crucial.
A cultural diagnostic for a sustainable transformation
During a Lean transformation, it is essential to take a proactive approach. The compass provides the means to deploy Lean management more effectively.
A proactive approach requires the determination of both the current state and the objective to be achieved during the first phase of the audit. The diagnosis traditionally focuses on the technical principles of Lean (JIT, Jidoka, etc.) and the management of human dimensions (leadership, skills, etc.). It provides:
-
an assessment of the current situation (maturity level)
-
levers to gain maturity
-
topics that require special attention to integrate the Lean philosophy
The Lean cultural compass proves to be valuable support during this diagnosis. It offers cultural indicators highlighting the contrast of the positioning and Lean culture.
These indicators target 10 predominant cultural dimensions such as the following: decision-making, application of rules, reflection process, time management, etc.
This cultural gap analysis promotes:
-
a better understanding of the actors’ values involved, in terms of the expected behaviors within the said culture.
-
better management of interpersonal relationships. (no blaming or shaming, etc.).
-
openness to exchange and awareness of cultural issues (consensus, empowerment, etc.)
-
setting higher standards and processes.
Including Lean values into your organizational culture will not only support Lean transformation, but will also be a key factor for success because it ensures the sustainability of the business model of your company.
[1] Cultural dimensions are derived from empirical studies, mainly conducted in the fields of ethnology, anthropology, sociology, ethnology, and linguistics.
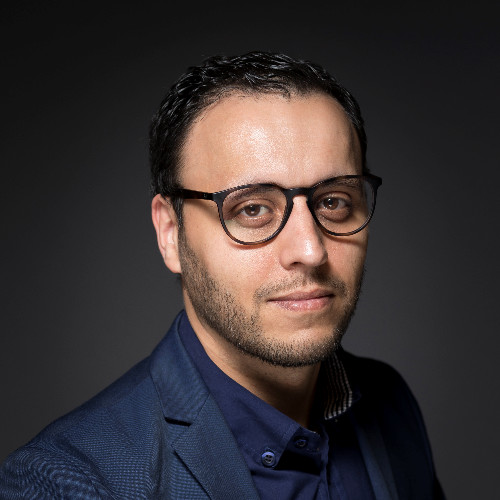
Mohand Hammoum
Ambassador of Business Improvement, Mohand is an experienced Industrial Leader, Certified Master Black Belt, and Accredited Trainer. He has built a professional experience in various industries (automotive, luxury, energy, banking, etc.) and has developed an expertise in Change Management in multicultural environments (Asia, Europe, the Middle East, and Africa, the Americas).
Post photo : Garrett Sears, Unsplash