Learn
Make culture become an asset in your Lean journey
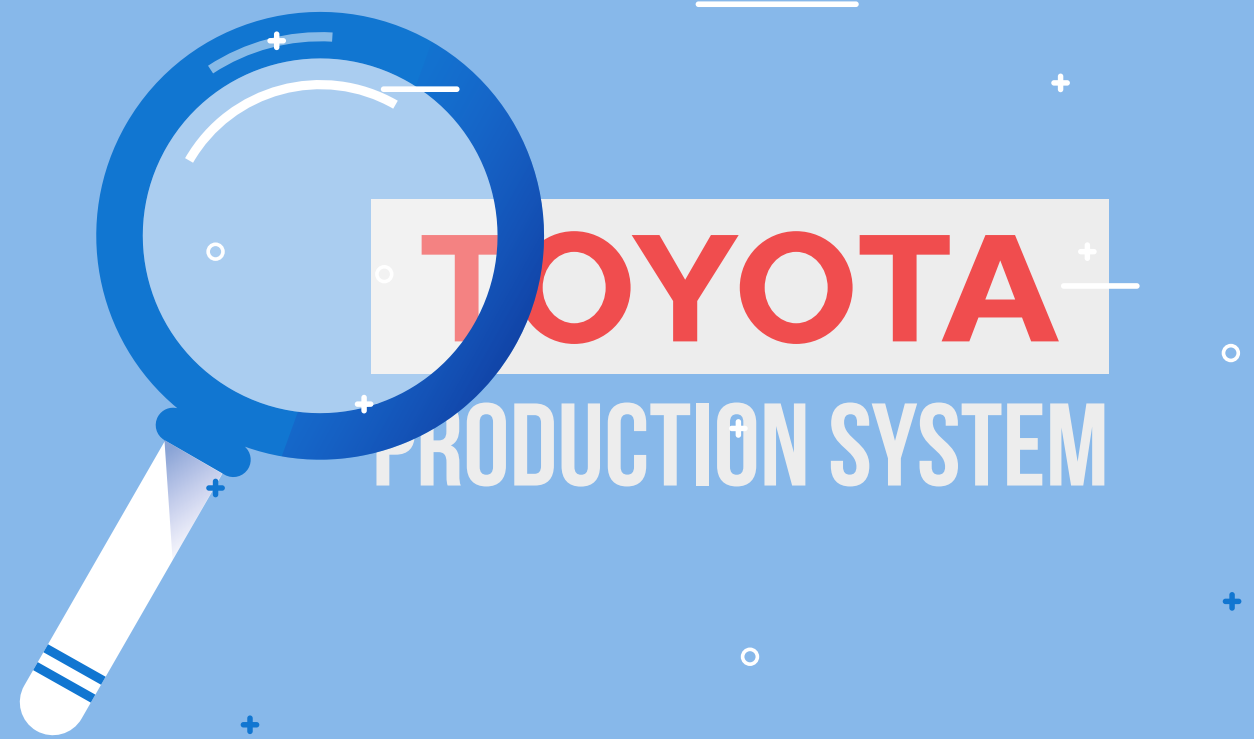
Lean & Toyota
Did you ever wonder why Toyota Production System (TPS) – later popularized by the name of Lean – is one of the most benchmarked business improvement strategies in modern industry?
Not only fortune 50 companies globally have adopted the TPS, but many others have designed their own production systems accordingly. However, only a select few have managed to achieve the impressive results of the car manufacturer.
TPS (the Toyota Production System) was inspired by Toyoda Group’s expertise in loom automation, but also from various methods implemented elsewhere, such as Ford’s production flows, Taylorism, Deming’s quality control concepts, or the inventory management of American supermarkets.
It is interesting to note that Japanese car manufacturers, Toyota and Nissan have both acquired their automotive production expertise in the United States. But while Nissan went with Ford’s mass production system, making very little changes to it, Toyota adapted it, by taking into consideration the strengths and weaknesses of the Japanese context, with its diverse and fragmented market that required greater flexibility.
Reflecting Toyota’s international success, the book “The Machine That Changed the World ”, started spreading the concept of Lean management around the world in the ’90s. The term Lean Manufacturing – according to the TPS methodology – became widely known.
Lean methodologies take a global and dynamic view of systems: placing individuals at its center, and integrating progressively better practices. Holistic and dynamic approaches are deeply rooted in Japanese culture. The use of Japanese terminology in Lean is not trivial. Language is a major prism in our vision of the world, and therefore by using their own language, employees at Toyota Japan can, for example, grasp more effectively the realities behind words and concepts than their foreign counterparts.
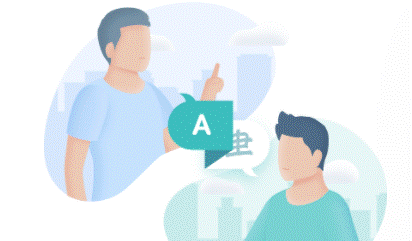
Bias
“If you are going to do TPS (Toyota Production System), you must do it all the way. You also need to change the way you think. You need to change how you look at things”.
Taiichi Ohno
Although the perception is the result of thought-structuring elements such as attributes (gender, origin, religion, language…) and experiences (training, studies, encounters…), human beings tend to consider their perception is shared by all. Lean is no exception to the rule …Our vision of the world shapes our beliefs, which in turn shape our behaviors.
The Lean cultural concept contextualizes itself by exposing the reference framework of its actors. First, the prism of Lean’s “architects” are Japanese and Toyotist. Then comes the perspectives of the leaders deciding to deploy Lean, and of Lean “practitioners”. Lean is a learning process, a way of thinking about the current situation, and how to improve it through tools and methodologies. Applying best practices that have been proven elsewhere, without consideration of local context creates a serious drift that hinders problem-solving. Ready-made solutions treat symptoms at best.
Addressing Lean as a culture, in and of itself, opens new perspectives. Like any other culture, Lean is complex and has its own practices (habits and customs). For a large number of cultural dimensions, we could rank its culture next to national cultures (hierarchical distance, decision-making, applying the rules, time management, etc.). Cultural orientations might positively or negatively impact routines and processes. For people to adopt a new work culture, they have to understand their own cultural frame of reference and share their vision of the new culture. Not only does a Lean approach need to be implemented into a national culture, but the company’s culture is also to be considered. The “House of Lean” is a comprehensive ecosystem with people at its center, which means that cultural paradoxes exist that have to be managed.
Identifying those delta’s and implementing strategies to integrate them within Lean rollout is key to success!
In addition to an in-depth understanding of Lean, the acquisition of cross-cultural expertise is a surefire way to learn how to revise one’s “thinking” as Taiichi Ohno – a pioneer of TPS – advocates. This form of expertise promotes humility and teaches one the ability to recognize one’s lens of the world, leading a person, by the same reasoning, to broaden their view of the world and others.
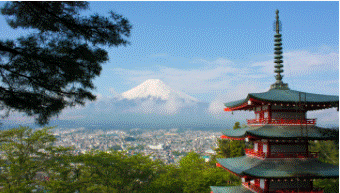
Lean & Japan
There is no Japanese “cultural drive” towards Lean, and it would be wrong to believe that its practices are intrinsically an expression of Japanese culture. Evidence for this is that Lean methodologies are not more present in Japan than elsewhere. This having been said, Lean philosophy has been shaped through an exclusive reading grid when it was designed by Japanese engineers working at a specific company: Toyota.
Could Lean management be implemented, in its original form, beyond the borders of Japan?
Toyota has been able to implement its Toyota Production System in 52 plants across 27 countries. The group applied TPS to different contexts, training local employees and even improving it by some of its foreign subsidiaries. In the book Toyota Culture, Jeffrey Liker explains that one of the main challenges during the company’s expansion was to find the right balance between adapting its system to the local context without neglecting its philosophy. For every new plant opening abroad, Toyota applied the Sensei method, by sending teams of Japanese TPS mentors to train their new colleagues on the group’s methodology. These subsidiaries eventually implemented hybrid models without compromising the fundamental principles. This adaptation was a success, as the results of Toyota’s foreign plants have been just as impressive as those in Japan.
Not every organization has the time or resources to hire a team of Japanese TPS experts. And it wouldn’t be that relevant while considering the diversity of industries applying Lean. However, taking some time to study the cultural aspect of Lean will provide the keys for a successful implementation. Once cultural strengths and weaknesses are identified, organizations can lead the change by making the necessary adjustments and allocating resources more efficiently. And as soon as direction is set and teams are on the same page, the Gemba can suggest adaptation – in line with the local context – enabling a sustainable transformation.
Ultimately, Lean is mainly concerned with reflection. It uses a systemic perspective and a bit of common sense. Its practice develops the ability to go beyond cognitive bias to address issues from a technical perspective.
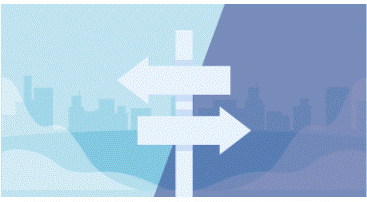
Systemic and analytic approaches
Science and concepts are approached and built-in relation to the cultural context in which they arise. Medicine is the perfect example on how culture has influenced its approach.
On the one hand, we have Western medicine that divides the body into separate parts, to study how each individual organ functions biologically. Whereas, on the other hand, Chinese medicine is based on a holistic vision, considering the human body as a whole. It aims at regulating the Tchi, a stream of energy flowing through the body, whose mission is to ensure that every organ (the microcosm) is in tune with the whole body (the macrocosm, the individual, the universe). Both approaches have their advantages and are, in fact, compatible.
Intercultural studies first started in the West, more specifically in Europe and the United States. Their approach was purely analytical, data and cultural dimensions were both separated and classified based on different scales, often unrelated to each other. Nevertheless, this fragmented approach has several benefits. Identifying, analyzing and classifying elements of accepted and expected behaviors within a culture, makes it easier to understand and identify cultural differences. The next step is understanding interculturality within a dynamic context.
In contrast, Lean was shaped within Japan’s holistic culture. While Frederick Winslow Taylor – the founder of Taylorism – separated planning from production, Taiichi Ohno – the founder of Lean – united them. Both contributions have been paramount to Lean, Taylor’s study of time and movement as well as standardization of work, and Ohno’s study on interdependence and the human dimension.
The cultural concept of Lean combines these two approaches: bringing together the cultural dimensions within a multidimensional prism.